Francouzský institut pro solární energii INES vyvinul nové PV moduly s termoplastikami a přírodními vlákny pocházejícími v Evropě, jako je lněný a čedič. Cílem vědců je snížit environmentální stopu a hmotnost solárních panelů a zároveň zlepšit recyklaci.
Recyklovaný skleněný panel na přední straně a prádlo na zadní straně
Obrázek: GD
Z PV časopisu Francie
Vědci z francouzského národního institutu pro solární energii (INES)-rozdělení francouzské alternativní komise pro atomovou energii (CEA)-vyvíjejí solární moduly s novými biologicky založenými materiály na přední a zadní straně.
"Vzhledem k tomu, že se uhlíková stopa a analýza životního cyklu nyní staly základními kritérii při výběru fotovoltaických panelů, se získávání materiálů v příštích několika letech stane klíčovým prvkem v Evropě," řekl Anis Fouini, ředitel CEA-ines , v rozhovoru s PV Magazine France.
Aude Derrier, koordinátorka projektu výzkumného projektu, uvedla, že její kolegové se podívali na různé materiály, které již existují, aby našli ty, které by mohly umožnit výrobcům modulů produkovat panely, které zlepšují výkon, trvanlivost a náklady, a zároveň snižovat dopad na životní prostředí. První demonstrator se skládá ze solárních článků heterojunkcí (HTJ) integrovaných do všeho složského materiálu.
"Přední strana je vyrobena z polymeru naplněného ze skleněných vláken, který poskytuje průhlednost," řekl Derrier. "Zadní strana je vyrobena z kompozitu na základě termoplastů, ve kterých bylo integrováno tkaní dvou vláken, lněného a čediče, což zajistí mechanickou pevnost, ale také lepší odolnost vůči vlhkosti."
Lon pochází ze severní Francie, kde je již přítomen celý průmyslový ekosystém. Čedič je získán jinde v Evropě a je tkaný průmyslovým partnerem Ines. To snížilo uhlíkovou stopu o 75 gramů CO2 na Watt ve srovnání s referenčním modulem stejného výkonu. Hmotnost byla také optimalizována a je menší než 5 kilogramů na metr čtvereční.
"Tento modul je zaměřen na střešní PV a integraci budov," řekl Derrier. „Výhodou je, že je přirozeně černá barva, aniž by bylo nutné. Pokud jde o recyklaci, díky termoplastikám, které lze přemístit, je oddělení vrstev také technicky jednodušší. “
Modul lze provést bez přizpůsobení proudových procesů. Derrier uvedl, že myšlenkou je převést technologii na výrobce bez dalších investic.
"Jediným imperativem je mít mrazničky pro ukládání materiálu a nezahájení procesu zesítění pryskyřice, ale většina výrobců dnes používá prepreg a je již pro to vybavena," uvedla.
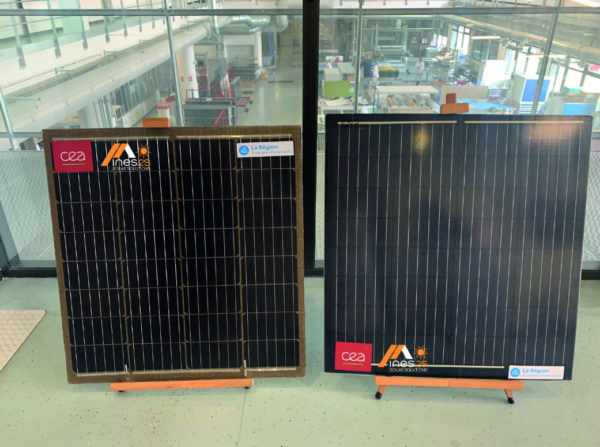
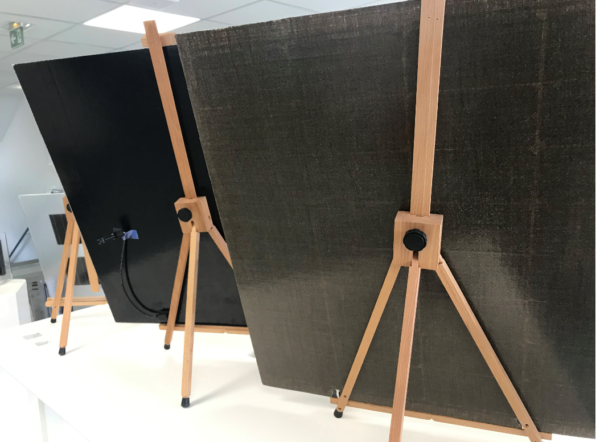
"Pracovali jsme na druhém životě skla a vyvinuli jsme modul složený z opětovného 2,8 mm skla, které pochází ze starého modulu," řekl Derrier. "Použili jsme také termoplastický enkapsulant, který nevyžaduje zesíťování, které bude proto snadno recyklovat, a termoplastický kompozit s lněným vláknem pro odpor."
Zadní strava modulu bez čediče má například přirozenou barvu povlečení, která by mohla být pro architekty esteticky zajímavá z hlediska integrace fasády. Kromě toho nástroj pro výpočet INES vykazoval 10% snížení uhlíkové stopy.
"Nyní je nezbytné zpochybnit fotovoltaické dodavatelské řetězce," řekl Jouini. „S pomocí regionu Rhône-Alpes v rámci plánu mezinárodního rozvoje jsme proto šli hledat hráče mimo solární sektor, aby našli nové termoplastiky a nová vlákna. Také jsme přemýšleli o současném laminovacím procesu, který je velmi energeticky náročný. “
Mezi tlakem, lisováním a chladicí fází, laminace obvykle trvá 30 až 35 minut, s provozní teplotou přibližně 150 ° C až 160 C.
"Ale pro moduly, které stále více zahrnují ekologické materiály, je nutné transformovat termoplasty při přibližně 200 ° C až 250 ° C, protože vědí, že technologie HTJ je citlivá na teplo a nesmí překročit 200 ° C," řekl Derrier.
Výzkumný ústav se spojuje s francouzskou indukční termokompresní specialistou Roctoolem, aby zkrátil doby cyklu a vytvořil tvary podle potřeb zákazníků. Společně vyvinuli modul se zadní plochou vyrobenou z polypropylenového termoplastického kompozitu, ke kterému byla integrována recyklovaná uhlíková vlákna. Přední strana je vyrobena z termoplastů a skleněných vláken.
"Indukční termokomprese Roctoolu umožňuje rychle zahřát dvě přední a zadní destičky, aniž by musel dosáhnout 200 ° C v jádru HTJ buněk," řekl Derrier.
Společnost tvrdí, že investice je nižší a proces by mohl dosáhnout doba cyklu jen několik minut, zatímco využívá méně energie. Tato technologie je zaměřena na výrobce kompozitních, aby jim poskytla možnost produkovat části různých tvarů a velikostí a zároveň integrovat lehčí a odolnější materiály.
Čas příspěvku:-24-2022